

The outside of the hood will more than likely be nice smooth surfaces, but the underside of the hood will not have such care taken when making the surfaces. Think of a hood on a car as being a solid model.

There is no industry standard for Class A surfaces. I look at most cell phones & I think I'd start off with a block & trim it away with surfaces. However you could get away with Edge Blends. The phone's exterior will probably be Class A surfaces with some nice curvature continuity in the blends. The blades will be the freeformed part more than likely.Ħ. However there are some very complex wheel designs that require a lot of surfacing prior to sewing into a solid.ĥ. I design wheels for a living & I normally use hybrid modeling. Car body surfaces are usually referred to as Class A (having no imperfections & smooth transitions from one surface to the next surface).Ĥ. Freeform (because there's probably going to be curvature (G2) or higher continuity). If there's any sort of funneling or transitional surfaces, you'll have to use Hybrid Modeling & use surfaces that extend all the way through the solid to trim off the freeform looking areas.ģ. This will depend on the complexity of the block, but I'd try it as Boolean first. Hybrid (Freeform with sweeps, extrudes, revolves & blends/chamfers)Ģ. That's just the problem.I don't know what the parts require as far as modeling necessities.are the blends tangent or is there a need for curvature(G2) or higher continuity for any of the parts? I would have to see the parts & have some design or styling input to come to a closer solution.ġ.

RE: Modeling, surface & solid CFDruss (Automotive) This is an excellent example of hybrid modeling. Just to give you a bit more clarification on cowski's modeling method, it sounds like he has a solid model but uses freeform surfaces that intersect the solid to trim away chunks & incorporate an area of that freeform surface into the solid. I feel only experience will lend a hand when it comes to deciding which is the best approach for the parts that you model. However there are times when you are forced to use freeform/surfacing to get your solid. I typically try to stick with solids as much as possible due to edge tolerancing affecting downstream applications like FEA. Finally, you can use a bit of a hybrid approach that uses both boolean/feature operations and surfacing to end up with a solid at the end. Other parts are easier to do completely as surfaces then trim & sew all the surfaces into solids. Some parts are easier to create from simple shapes & use boolean (unite, subtract & intersect) operations along with draft, blends & chamfers.
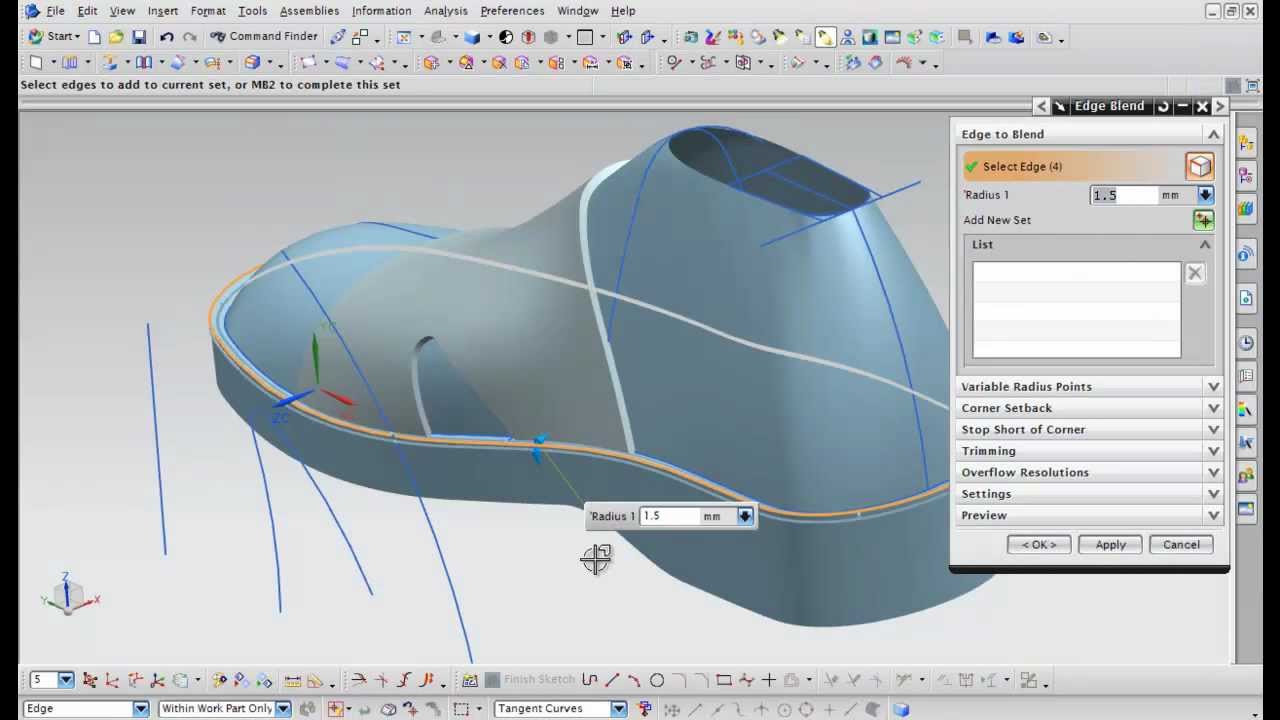
Inserting the components in a product file
#UG NX SURFACE SOFTWARE#
Understand the Modeling software interface
